The Science Behind Porosity: A Comprehensive Overview for Welders and Fabricators
Understanding the complex devices behind porosity in welding is critical for welders and producers aiming for impeccable workmanship. From the composition of the base products to the intricacies of the welding process itself, a wide range of variables conspire to either intensify or relieve the existence of porosity.
Understanding Porosity in Welding
FIRST SENTENCE:
Examination of porosity in welding reveals vital insights into the honesty and top quality of the weld joint. Porosity, characterized by the visibility of dental caries or spaces within the weld metal, is a typical worry in welding processes. These spaces, otherwise appropriately resolved, can endanger the architectural stability and mechanical residential properties of the weld, resulting in potential failures in the finished product.
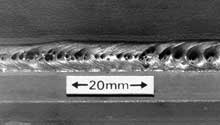
To spot and measure porosity, non-destructive screening techniques such as ultrasonic testing or X-ray assessment are usually used. These techniques permit the recognition of interior defects without endangering the honesty of the weld. By evaluating the dimension, shape, and circulation of porosity within a weld, welders can make informed choices to boost their welding procedures and attain sounder weld joints.
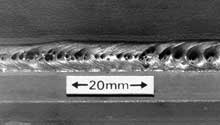
Factors Affecting Porosity Development
The incident of porosity in welding is influenced by a myriad of aspects, varying from gas protecting performance to the complexities of welding specification settings. Welding parameters, including voltage, existing, take a trip speed, and electrode type, also impact porosity formation. The welding technique used, such as gas steel arc welding (GMAW) or protected metal arc welding (SMAW), can influence porosity formation due to variants in warm distribution and gas coverage - What is Porosity.
Results of Porosity on Weld Quality
Porosity formation dramatically compromises the structural stability and mechanical residential properties of welded joints. When porosity exists in a weld, it creates voids or tooth cavities within the product, lowering the general strength click here for info of the joint. These voids serve as anxiety focus points, making the weld extra susceptible to splitting and failing under tons. The presence of porosity likewise weakens the weld's resistance to corrosion, as the trapped air or gases within the spaces can react with the surrounding setting, leading to deterioration gradually. Additionally, porosity can prevent the weld's capability to stand up to stress or influence, further endangering the overall quality and dependability of the get redirected here welded structure. In critical applications such as aerospace, automotive, or structural buildings, where safety and security and longevity are vital, the damaging impacts of porosity on weld high quality can have severe repercussions, Resources emphasizing the significance of reducing porosity via appropriate welding strategies and procedures.
Strategies to Decrease Porosity
To improve the quality of welded joints and guarantee structural stability, welders and fabricators employ particular strategies focused on reducing the formation of gaps and tooth cavities within the product during the welding procedure. One effective approach to minimize porosity is to make certain proper product prep work. This includes comprehensive cleaning of the base metal to remove any kind of impurities such as oil, oil, or wetness that can add to porosity formation. Furthermore, utilizing the proper welding parameters, such as the proper voltage, current, and travel rate, is vital in stopping porosity. Maintaining a regular arc size and angle during welding additionally helps in reducing the likelihood of porosity.

Moreover, choosing the best securing gas and keeping appropriate gas flow rates are crucial in minimizing porosity. Utilizing the ideal welding strategy, such as back-stepping or employing a weaving movement, can also assist disperse heat uniformly and lower the chances of porosity development. Making certain correct ventilation in the welding setting to eliminate any kind of potential sources of contamination is important for achieving porosity-free welds. By applying these methods, welders can successfully minimize porosity and generate premium bonded joints.

Advanced Solutions for Porosity Control
Executing sophisticated technologies and cutting-edge methods plays a critical role in accomplishing remarkable control over porosity in welding procedures. Furthermore, using sophisticated welding techniques such as pulsed MIG welding or modified ambience welding can also assist minimize porosity concerns.
Another innovative service entails the usage of advanced welding devices. Making use of devices with integrated features like waveform control and sophisticated power sources can boost weld quality and minimize porosity dangers. The implementation of automated welding systems with accurate control over specifications can substantially reduce porosity defects.
Additionally, incorporating advanced monitoring and examination innovations such as real-time X-ray imaging or automated ultrasonic screening can assist in spotting porosity early in the welding procedure, enabling instant corrective actions. Generally, integrating these sophisticated solutions can considerably improve porosity control and enhance the overall top quality of bonded components.
Verdict
In final thought, comprehending the science behind porosity in welding is essential for welders and producers to generate premium welds - What is Porosity. Advanced options for porosity control can even more improve the welding process and guarantee a solid and trustworthy weld.